November 26, 2018
Should ship owners and port operators be concerned at the risk of mooring equipment failure on board moored vessels?
I was recently directed to an online a paper presented at a forum hosted by Pilbara Ports. According to the paper, there have been a significant number of equipment failures during towing and mooring operations. Over a two-year period, there was an average of 3-5 Mooring Line Incidents (2015-2017) per month. Of these incidents, 7% were at the winch end, 62% at the fairlead and 22% at the hook end.
Accordingly, Pilbara Ports acted and issued a safety notice including new requirements (https://www.pilbaraports.com.au/PilbaraPortsAuthority/files/de/de697582-96aa-492e-8408-833f3c3e0515.pdf) .
In my capacity as marine consultants we often find ourselves working with the rated capacity of ship equipment for mooring and related marine operations and often find the rating is not valid or workable. When reviewing the latest OCIMF MEG4 guidelines I found some context to the discussion.
Marine Equipment Guidelines (MEG4) includes a statement “It is important to remember pre-2007 tankers were not subject to any unified Classification Society guidelines on the attachment of mooring/towing fittings to the tanker structure, so the actual SWL of the mooring/towing fittings on these ships may not be as high as the certified value. For such tankers, OCIMF has consistently recommended that an engineering assessment be undertaken of the deck mounting and support structure.”
It seems that OCIMF recognise, what we have been experiencing for years, there has been an inherent weakness in mooring connections and fittings on Class approved vessels. We have found capacity differences when checking existing vessel fittings and structures against their marked capacity for tow and mooring operations in offshore applications. In these applications, there is misalignment when the design of the fittings has been based on the MBL of the mooring line or equipment number as per the ship design standards, when compared with a peak mooring load, position keeping or tow load.
In the offshore context there arises a raging argument as to what is expected to fail first and how is the equipment adequately designed, tested and fixed to provide confidence to the users that such an approach or philosophy can be adopted.
In respect to ship fittings, the International Association of Classification Societies (IACS) provides a governing document with alignment to Classification Societies. However, the onus is on the Classification Society to request that designers undertake the necessary engineering justification to support approval and marking of the equipment.
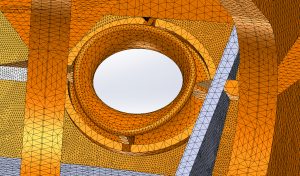
Meshing Closed Chock Geometry.
Often the fitting is already type approved with a tested manufactured rating. The question then becomes how to fix the equipment to a ship structure while maintaining load path continuity and how to test to ensure the structure fixing (welding) is adequate. In the shipping world, this comes back to only greater scrutiny of welding specification, quality and acceptance. This is despite the highly loaded nature of the supporting structures.
One of our industry defaults is to provide an adequate load test. NDT the weld before, proof load test and then NDT again. If the structure passes i.e. no weld cracks or failures evident, then we are ready for painting and stamping ratings. Occasionally, in exceptional circumstances driven by the practicality of load testing and NDT, load capacity can be approved through engineered design. Usually this requires significant engineering justification (cost) as utilisation of all members must be demonstrated as low as possible through extensive analysis demonstrating low risk levels.
Proper analysis and engineering judgment can be costly and subjective at times. Spending money on “unnecessary” engineering is not a ship owner’s priority. However, Incidents currently experienced in the industry are triggering internal risk processes, and a review of how necessary is proper analysis and engineering judgement.
ONA Consultants is well placed to analyses and provide engineering support verification and technical investigations of mooring and tow operations. Our experience and qualified hydrodynamic, mooring and marine structural engineers underpin these specialized services.